
聪明检验每一颗螺丝螺帽,三星科技用 AI 实现零缺陷管理
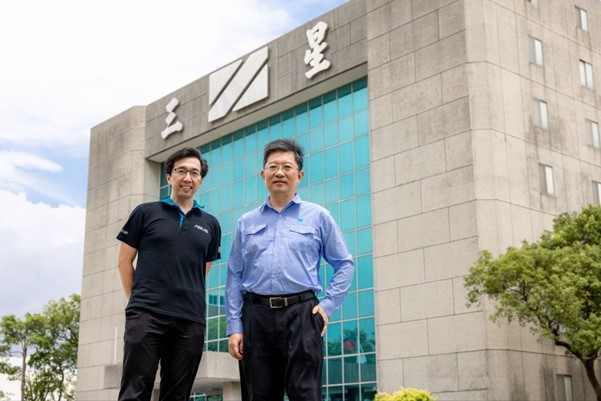
试想一下,一辆在高速公路上行驶的汽车,车内某个零部件在行驶过程中忽然松脱,将会造成什么样的后果?轻则影响车辆性能,严重就有可能危及人身安全,三星科技总经理陈信志指出,这就是汽车厂商为何会严格要求供货商确保产品质量的原因,「尤其是肩负连结紧固车内零部件之责的螺丝、螺帽,汽车厂商更是要求做到零缺陷,这就对扣件供货商的品检控管带来严峻挑战。」
对此三星科技在 2021 与华硕智能物联网合作导入 ASUS IoT AISVision,该AI机器视觉工具包在强化品检工作效能的同时,也让该公司研发团队拥有打造 AI 视觉检测系统的能力。
三星科技用不同营运思维走出红海市场
成立超过半世纪的三星科技是全球螺帽产业龙头企业,月产能高达 7,500 公吨,除了扣件外也自制自销螺丝、螺帽模具,车用螺帽的产量更位居世界第一,是台湾地区典型的隐形冠军。三星科技的发展视野向来宏远,早期就决定走出以价取胜的红海市场,转向高值化车用螺丝螺帽,不过此领域虽然无须价格竞争,还是有不同压力与挑战,也就是产品质量。
正如前文所叙,车商对螺丝、螺帽的要求是「零缺陷」,各种肉眼难辨的形状偏斜或看似不影响效能的脏污,全都会被要求退货。陈信志接着点出,现在汽车制造已经高度自动化,螺丝、螺帽一旦有瑕疵无法自动组装,整条产线会马上停工,「也就是说我们不检验,车厂也会帮你验,如果出问题,我们供货商的损失会更大,品牌信誉度也会受影响。」
对于车厂的零缺陷要求,三星科技早期以人力进行检测,后来导入外部技术支持,培训内部团队自行开发 AOI 视觉检测系统的能力。传统的 AOI 视觉检测系统为「Rule Based」模式,在系统建置初期,先依照既有经验设定瑕疵种类,在检验过程中发现不良品后立刻剔除,三星科技研发部经理杨耀隆指出,Rule Based 视觉检测系统有两大缺点,一是系统无法检出当初设定以外的瑕疵,不易应付扣件生产过程中产生的随机缺陷;二是为了达到零缺陷,检测条件设定必然严苛,「宁可错杀一百,也不放过一颗的结果就是误杀率过高,导致大量良品被丢弃,生产成本居高不下。」
近几年 AI 浪潮再起,并在制造领域逐步普及,三星科技认为 AI 与 AOI 的整合智能化检测系统会是上述问题的解方,经过一轮市场访查后,决定与华硕合作。陈信志提到华硕能在众多 AI 厂商中胜出有几大原因,首先是企业量体庞大,可确保长期提供服务,其次是专业技术与导入经验充足,他表示产业 AI 方案的采用门坎仍高,软硬件解决方案必须能有效满足使用者的特定需求,因此,双方接触初期是以三星出题、华硕解题的方式沟通,确保其专业经验可解决三星痛点。
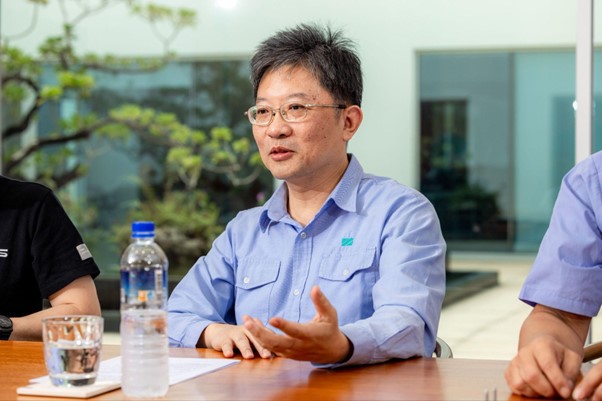
图说:三星科技总经理陈信志表示,对三星科技而言,华硕 AISVision 就像是 AI 种子,这颗种子会先在 AOI 检测结出第一颗智慧化果实。
第三则是华硕的 AISVision 具备二次开发功能。陈信志提到,三星从以前就强调设备自制,就像前面提到,无论是螺丝、螺帽模具或各种制造设备都不假手他人, AI AOI 也是如此。华硕的解决方案正可满足「授人以鱼,不如授人以渔」需求, AISVision 机器视觉工具包和 SDK(软件开发工具包)支持二次开发,可在系统顺利导入后,由三星研发团队接手负责后续厂内 IT 系统分检设备的整合、升级、改版与维护。
传统 AOI 误杀率过高,AI 其实可以自主判断瑕疵?
华硕智能物联网智能制造产品企划部副处长辜英宪指出,市场上很多方案所使用的 AI 应用架构相当复杂,为降低导入门坎,华硕 AISVision 将产业客户所需的多种工具整合为单一平台,并大幅简化二次开发难度,从而加速系统上线时程。
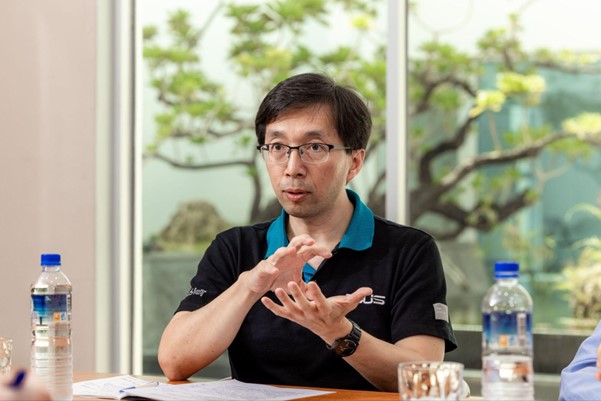
图说:华硕智能物联网智能制造产品企划部副处长辜英宪指出,市场上很多方案所使用的 AI 应用架构相当复杂,为降低导入门坎,华硕 AISVision 将产业客户所需的多种工具整合为单一平台。
以三星科技的系统为例,在建构训练数据集的阶段,AISVision 的自动标识(Auto Labling)功能,就可协助三星团队从大量的不良品影像中快速完成瑕疵标识,并在训练模式(Training Model)建立起有效模型,最后再将此逻辑移转产在线的 AI AOI 系统,系统内的推论模式(Inference Model)不仅可判别瑕疵,AISVision 还拥有学习能力,随着数据集的累积,进行模型再训练,持续优化模型,解决以往因 Rule Based AOI 不易调整,只能严苛设定检验条件,导致误杀率居高不下的问题。
除了 AISVision 的完整功能外,华硕的服务也是这次系统可以顺利上线的主要因素。陈信志表示,操作、使用 AOI 系统者都是 OT 人,不一定熟悉 AI 领域专业,因此导入阶段必须不断学习、沟通,华硕过去已协助众多不同类型制造业导入 AI 系统,充分了解过程中会遇到的挑战与解决方式,最后在华硕与三星研发团队的通力合作下,顺利完成所有的软硬件建置。
让 AI 串联全产线,第一步棋让华硕来协助!
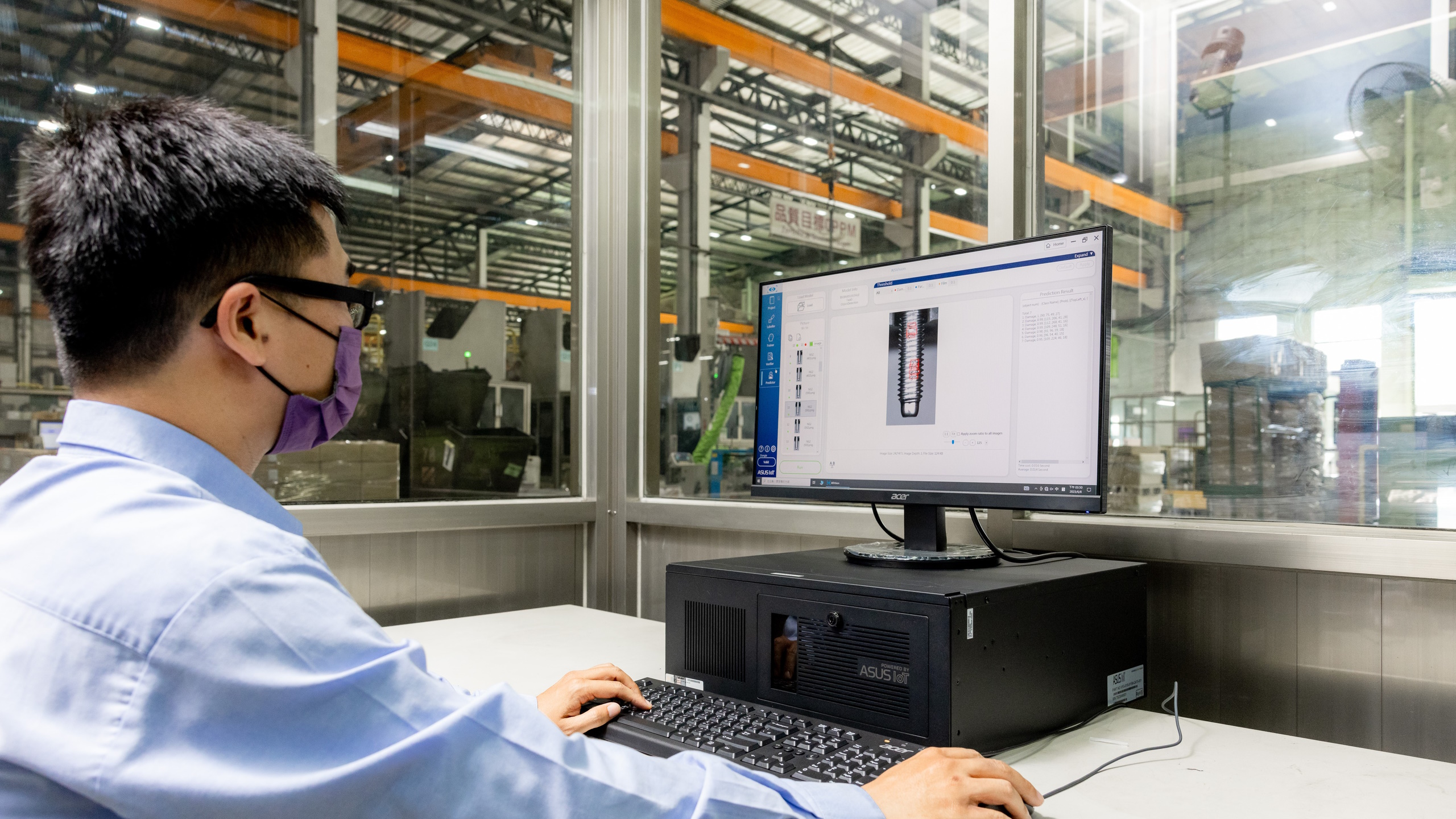
图说:华硕 AISVision 的自动标识(Auto Labling)功能,就可协助三星团队从大量的不良品影像中快速完成瑕疵标识。
2023 年 5 月,三星科技的 AI AOI 系统正式上线, AI 的智能检测效益正逐步浮现中。对于未来规划,杨耀隆表示会将 AI 系统的训练之责交给第一线,「我们希望让产线人员具备足够的 AI 专业,日后可自行依照需求调整架构,并藉由现场的瑕疵数据判断结果的回馈,重复训练 AI,让 AI 的判别越来越精准。」至于更长期的计划,则是将 AI 架构延伸到产线制程前端,例如记录、分析机台设备的扭力、振动等数据,此功能除了可调整机台参数、提升良率外,也能避免瑕疵品进入后续的加工流程,进一步减少制造成本的浪费。
陈信志表示,对三星科技而言,华硕 AISVision 就像是 AI 种子,这颗种子会先在 AOI 检测结出第一颗智慧化果实,「我认为这将启发其他部门对 AI 的想象,思考如何让 AI 成为自己的助手,提升工作效率,从而启动另一波升级,让三星持续保持竞争力。」